Tesla Engineering Ltd
Tesla Engineering conçoit et fabrique des aimants pour les accélérateurs de particules, des bobines à gradient spécialisées à utiliser dans les systèmes d'IRM et des aimants supraconducteurs avancés pour les marchés émergents tels que la fusion nucléaire, les sources d'énergie renouvelables, le traitement des semi-conducteurs et le traitement du cancer.
Fondée en 1973, Tesla a depuis ouvert des bureaux aux États-Unis et aux Pays-Bas, et dispose d'une solide équipe de plus de 300 personnes au Royaume-Uni seulement. Ayant rapidement augmenté de plus de 25 % au cours des deux dernières années, la charge de travail de Tesla a connu une augmentation spectaculaire, cependant, en raison de l'espace au sol limité dont ils avaient besoin pour trouver une solution pour rendre leurs machines actuelles plus efficaces.
John O'Shea, directeur de l'atelier d'usinage, a dirigé le projet de rationalisation de l'atelier d'usinage et a introduit la tenue de travail à changement rapide à Tesla. Après avoir recherché une variété de solutions de maintien du travail, John a contacté le directeur commercial de NIKKEN, Danny Wells, pour l'aider à trouver une solution.
Danny et l'équipe technique du centre d'innovation Nikken ont travaillé avec Tesla pour concevoir une solution qui maximiserait les capacités de la machine tout en minimisant les temps d'installation et de chargement, l'intervention de l'opérateur et qui réduirait le volume des copeaux.
La solution proposée se compose de rails TRIAG complets avec des modules d'étau PowerClamp, sur lesquels ils ont conçu et fabriqué des palettes de faces internes sur lesquelles le système de rails peut s'asseoir en dessous.
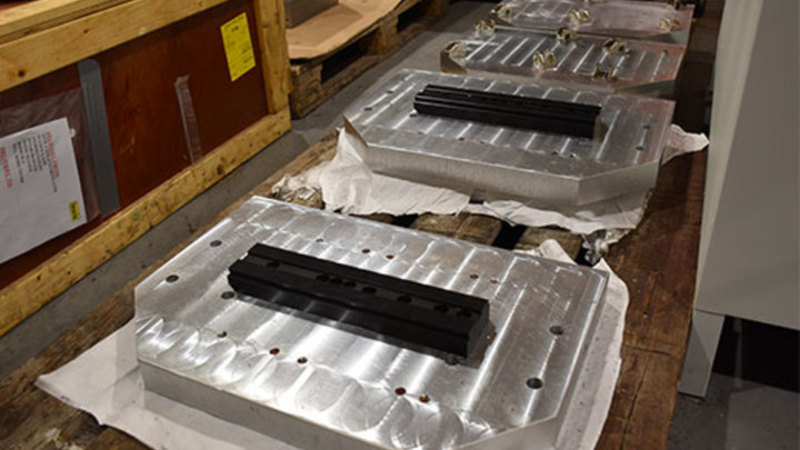
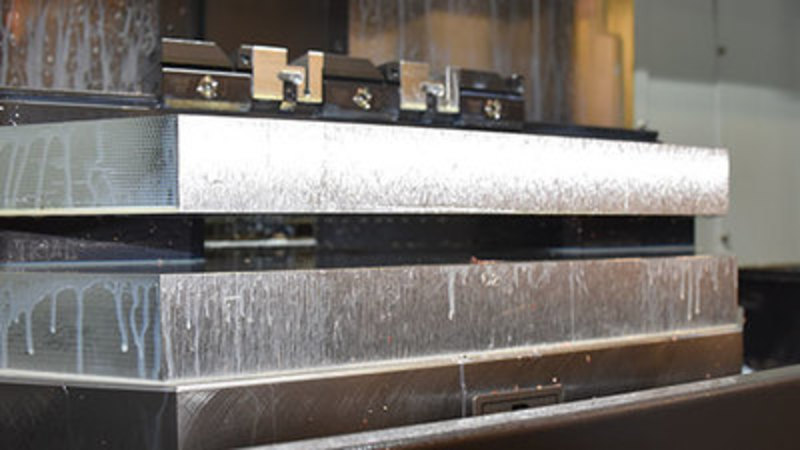
La solution permet à Tesla de monter et descendre les palettes de la machine sans aucun temps d'installation, la seule intervention de l'opérateur étant de changer les pinces en fonction du travail à effectuer. Tesla utilise actuellement 2 palettes sur une machine, ce qui signifie que pendant que l'opérateur charge une palette, la machine travaille sur l'autre palette.
Minimiser l'intervention de l'opérateur a eu un impact énorme sur la productivité de Tesla. Auparavant, il fallait 4 à 6 heures pour définir un travail, la solution de changement rapide leur permet désormais de le faire en seulement 15 minutes sans avoir à chronométrer la pièce ou à définir une référence, car la référence est déjà là.
La solution fournie est modulaire, ce qui signifie qu'elle peut être adaptée au travail à accomplir et fournit un couple de serrage élevé. Tesla usine une variété de matériaux, y compris le cuivre, de sorte que le couple de serrage élevé était un énorme avantage en raison du fait que les mâchoires de la pince n'avaient besoin de tenir que 3 mm de matériau, alors qu'auparavant, elles devaient tenir au moins 10 m. Encore une fois, ce qui entraîne des économies de coûts élevées.
« Notre temps d'installation moyen était de 4 heures et un temps de cycle de 25 % pour le chargement. Grâce à la nouvelle solution de serrage des pièces, nous sommes maintenant 50 % plus efficaces.» John O'Shea
Depuis qu'il utilise cette nouvelle solution, Tesla est devenu plus efficace au point de manquer de matériaux en raison de la vitesse de production. Depuis qu'il a prouvé que cette solution fonctionne sur une machine plus petite, Tesla déploiera la solution sur une variété de machines, ce qui réduira considérablement le gaspillage de matériaux coûtant jusqu'à 125 000 £ (146 000 €).
Pour plus d'informations sur l'optimisation de votre ligne de production, n'hésitez pas à contacter notre équipe d'experts pour une consultation.