X-CEL SUPERTURN LTD
Fournissant des solutions de haute qualité à une clientèle mondiale, X-Cel Superturn Ltd est spécialisée dans les composants usinés avec précision dans les secteurs de la pétrochimie (y compris le forage de fond, les applications de surface et sous-marines), la production d'électricité, l'aérospatiale et la construction.
X-Cel a consulté Nikken pour une future application d'usiner 31 trous de 3 mm de diamètre à une profondeur de 44 mm à l'intérieur d'un composant.
Cela a mis en évidence le besoin d'une solution de tête d'angle à 90° pour fournir l'angle d'approche nécessaire pour atteindre ces caractéristiques, en utilisant leur centre d'usinage horizontal Doosan NHM, en combinaison avec les opérations de fraisage supplémentaires nécessaires pour le reste de la pièce.
Actuellement, ce type de travail nécessiterait 2 réglages sur 2 machines différentes (la machine horizontale pour l'opération initiale avec une deuxième opération étant réalisée sur un centre d'usinage vertical). La solution NIKKEN/ALBERTI avait le potentiel de permettre un seul réglage sur la machine horizontale avec la tête d'angle offrant une approche d'usinage similaire à celle de la machine verticale.
NIKKEN a recommandé sa solution d'optimisation de broche ultime, offrant le BT50-TH90cn-3.5 avec une sortie en serrage SLIM CHUK NIKKEN. Cela permet efficacement au client d'utiliser les avantages des solutions de pinces et d'écrous de précision de NIKKEN Slim Chuck. Non seulement cette combinaison améliore considérablement la précision et les performances, mais la tête angulaire est également capable de fournir une capacité maximale de 100 bars grâce au liquide de refroidissement de la broche.
Le principal avantage pour le client est que, lorsqu'il est utilisé avec le système d'arrosage Type "JET" et la coiffe appropriée, le liquide de refroidissement peut être contrôlé à travers ou autour de l'outil coupant.
NIKKEN a également fourni la solution d'outillage sous la forme d'une tête à changement rapide d'outil, permettant à l'opérateur de changer automatiquement l'outil de la tête lorsqu'il en a besoin, ce qui permet d'économiser davantage de temps de configuration sur la machine.
En conjonction avec le changement de palette sur la machine et l'environnement de coupe amélioré grâce à la tête Alberti, les temps de cycle ont été considérablement améliorés, passant d'un peu plus d'une heure à 8 minutes, mais également en économisant davantage en offrant une capacité d'usinage supplémentaire sur une VMC !
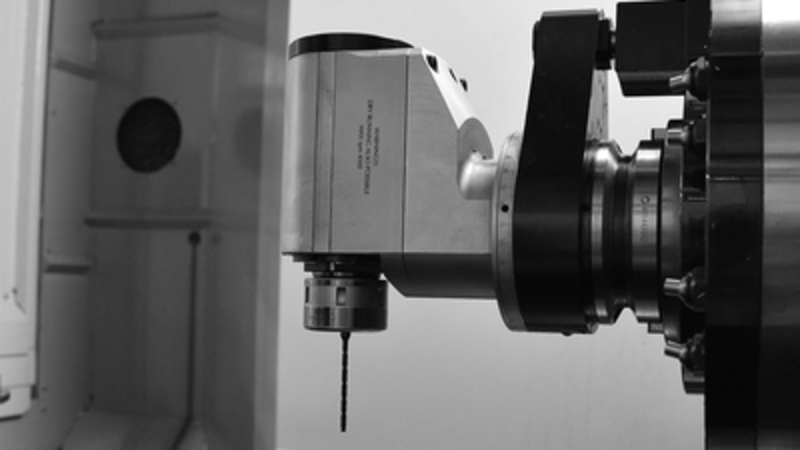
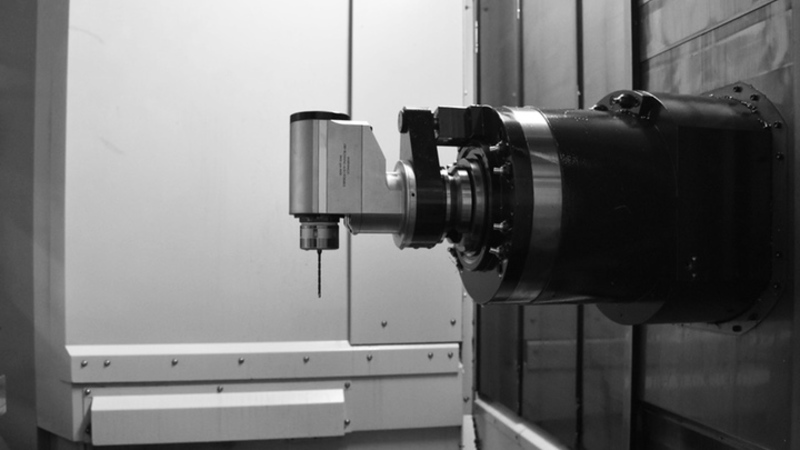